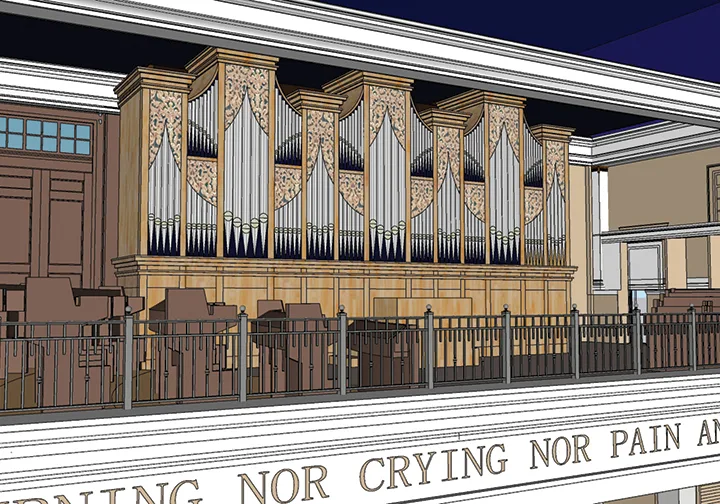
by Joe Bollig
joe.bollig@theleaven.org
LEAWOOD — Call it a pipe dream, or rather, a pipe organ dream come true for St. Michael the Archangel Parish here.
It’s certainly a dream come true for Anne Dow and her fellow choir members. They sent corks popping when they learned that Opus 1, the parish’s long-awaited organ, would be built.
“We were very excited,” said Dow. “When the contract was finally signed, we literally broke out the champagne, we were so happy. And we toasted the St. John’s Abbey Organ Builders and sent the video to them.”
This past October, work began on the parish’s $1.68 million organ project at the newly established St. John’s Abbey Organ Builders in Collegeville, Minnesota. Leading the project is Martin Pasi, whose firm was absorbed into the new abbey organ building company.
Plans are for the new organ to be installed in the St. Michael choir loft in Spring 2025.
The new organ will have 3,204 pipes — the largest will be 16-feet tall; the smallest, 2-inches tall. It will be 30-feet wide, 10-feet deep and 17-feet high. It will be made of solid white oak and metal alloys of lead and tin. It will weigh 10 tons.
“It’s an absolute one-of-a-kind organ,” said Kevin Vogt, director of worship and sacred arts at the parish. “It’s somewhat of a challenging space to work in because there’s so much area in the choir loft but the ceiling is very low.
“Seventeen feet is a very low ceiling but it’s a very large church, so it needs a certain amount of volume and quite a bit of variety of sound or tone colors to make music effective in a large space like this to undergird congregational singing.”
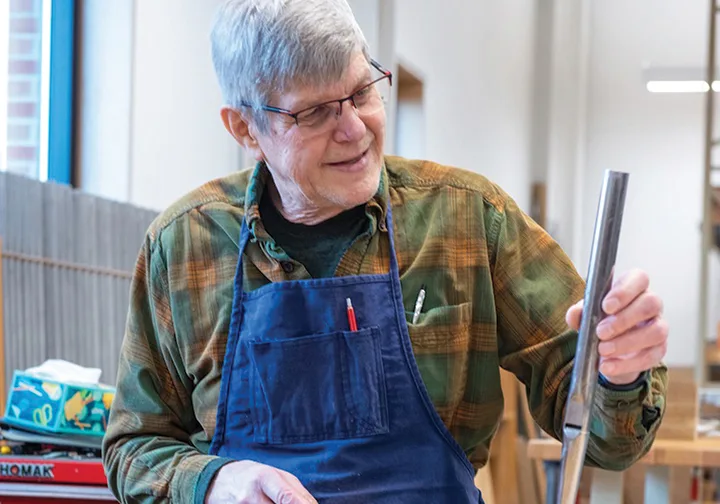
It would be nice to have a 32-foot bass pipe but that isn’t possible, so designers did other things with the organ design to compensate for the space it will occupy.
“One of the things that’s fun about it is that it has four sections we call divisions,” said Vogt. “One is played by the feet. Three other sections or divisions are played by each of the three keyboards by hand. Each of those three divisions will be set side by side because we have so much width to work with. Two on the side are intended for the accompaniment of voices.”
A long-range goal
Building this grand organ was always part of the plan.
“When the church was built in 2009, there were some things left unfinished,” said Vogt. “We left the choir loft unfinished, but it was always in the original plan that there would be an organ.
“We saved a little bit of money by getting a temporary organ from a church in Columbus, Ohio. So, we’ve had a little pipe organ, but it was designed for a church the size of a large garage. The Episcopal church we got it from was about that size.”
The present born-again Catholic organ, built in 1970, makes beautiful sounds, but it simply isn’t big enough for a church the size of St. Michael. It will be donated and moved in mid-February to Christ the King Parish in Kansas City, Kansas.
“The [present] organ has no scope whatsoever,” said Tom Zachacz, the parish assistant for music. “It’s not very expressive and is kind of monochromatic in sound. Even though we don’t need a lot of volume, when we do need the volume, it’s just not there. It sounds good in the room, but we need something that will activate the room.”
To get by until the new Opus 1 arrives in 2025, the parish will use a tiny “trunk” organ, nicknamed “the dinghy,” which is small enough to be moved around as needed.
The great tradition continues
There are a few reasons why this is a special organ and a special project.
This organ is being designed and built in the great European and Benedictine traditions of organ construction and use.
Pasi, now an American citizen, was born in Austria and learned the art and craft of organ design and construction there. He moved to the United States and, over the course of his career, established his own company — Pasi Organ Builders, south of Tacoma, Washington. Pasi’s company made 29 large, custom-built organs.
Vogt got to know Pasi when St. Cecilia Cathedral in Omaha, Nebraska, where he was music director, contracted Pasi to build an organ.
“We first became acquainted 25 years ago and have worked on several other organ projects together,” said Vogt.
Nearing retirement age, Pasi decided to pass on his knowledge and tools to the Benedictines at St. John’s Abbey, which already had a large woodworking and furniture-building shop.
The church has used the organ for sacred music for more than 1,000 years, and the Benedictine order has an organ-building tradition from about the ninth to the end of the 18th century.
The organ at St. Michael is the first to be built by St. John’s Abbey Organ Builders.
“The pipe organ as we know it is largely the result of technical developments over the last 1,000 years by Benedictine monks,” said Vogt, “but the St. Michael organ will be the first example of organ building by Benedictine monks since the French Revolution [of 1789].”
The organ will draw from that great European tradition.
“It’s a pipe organ with mechanical action,” said Vogt. “It has some electricity in it, a blower to provide the air to fill the large bellows, and the lights. But other than that, it doesn’t depend on electricity for anything. It’s all mechanical with a series of linkages made of wood, metal and carbon fiber. When you press a key down there are a series of mechanical linkages that go from the keyboard to the pipes.”
This is a very old way of making organs. The benefit of linkages is that the organist has a very fine control over how the pipes make their sounds. Also, it’s a simple technology. So long as the raw materials are available, repairs can be made.
“The technology of an organ like this was settled about 1750,” said Vogt. “Organs made this way have a great longevity. Some organs in Europe that are made in this traditional way have lasted for 300 to 400 years. There’s a bigger expense on the front end to make an organ this way, but in terms of longevity and ease of maintenance, it’s just about the most economical thing anyone can think of doing.”
The new Opus 1 at St. Michael can be thought of as a “generational gift,” said Vogt.
Even after the organ is built and installed, there’s still work to be done. In the future, Vogt plans for the construction of choir stalls on both sides of the loft, which will facilitate the prayer of the Liturgy of the Hours.
“Doctor Vogt designed an organ that’s basically like an 18th-century south German design,” said Zachacz. “Those organs feature a lot of different sounds, so there’s a lot of variety in the [music] they make.
“So finally, for the first time, we’ll have an organ that can not only accompany very effectively but can also play a wide variety of organ literature.”